Industrial Centrifugal Spary Dryer
- Model: LPG-10L
- Moisture Evaporation : 10Kg/H
- Power(kW): 20kW
- Temp. Accuracy: 0.1℃
- Length×Width×Height (m): 3.2x1.5x2.4
- Dry Powder Recovery Rate(%): ≥95
Ideal for small labs and production, the LPG-10L centrifugal spray dryer efficiently transforms liquids into powders. With a 10L capacity and precise drying, it's perfect for chemical research and small-scale manufacturing.
Introduction
The LPG-10L centrifugal spray dryer stands as an outstanding representative of modern liquid forming and drying technology. With its high efficiency, precision, and flexibility, it has shown broad application prospects in various fields such as chemicals, food, pharmaceuticals, and material sciences. This equipment is specifically designed to handle solutions, emulsions, suspensions, and paste-like materials, rapidly converting these liquid raw materials into powder, granule, or block solid products. It meets the market's high standards for precise particle size distribution control, low residual moisture, ideal bulk density, and specific particle shape.
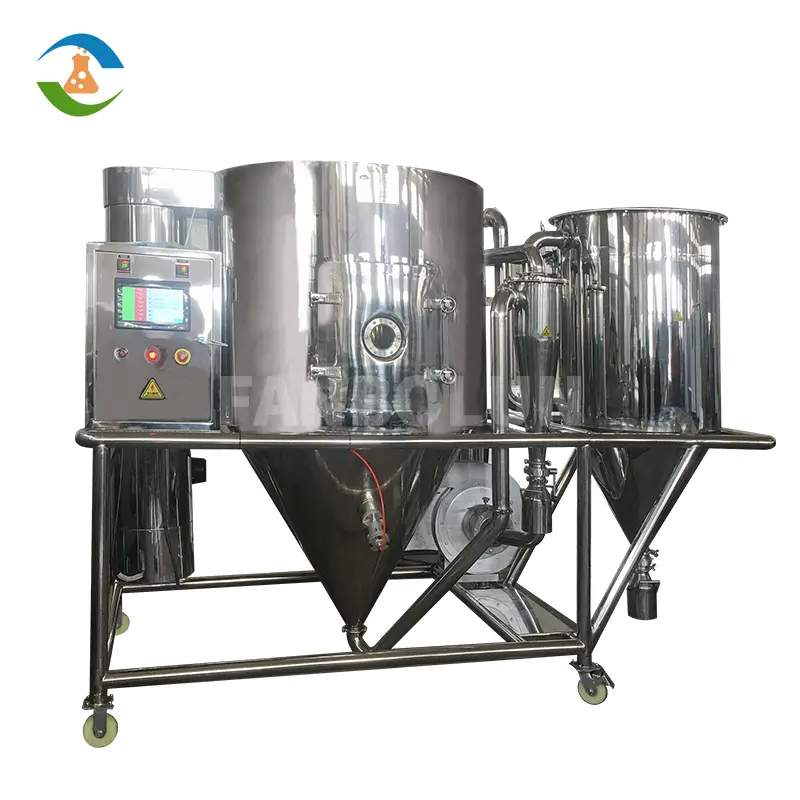
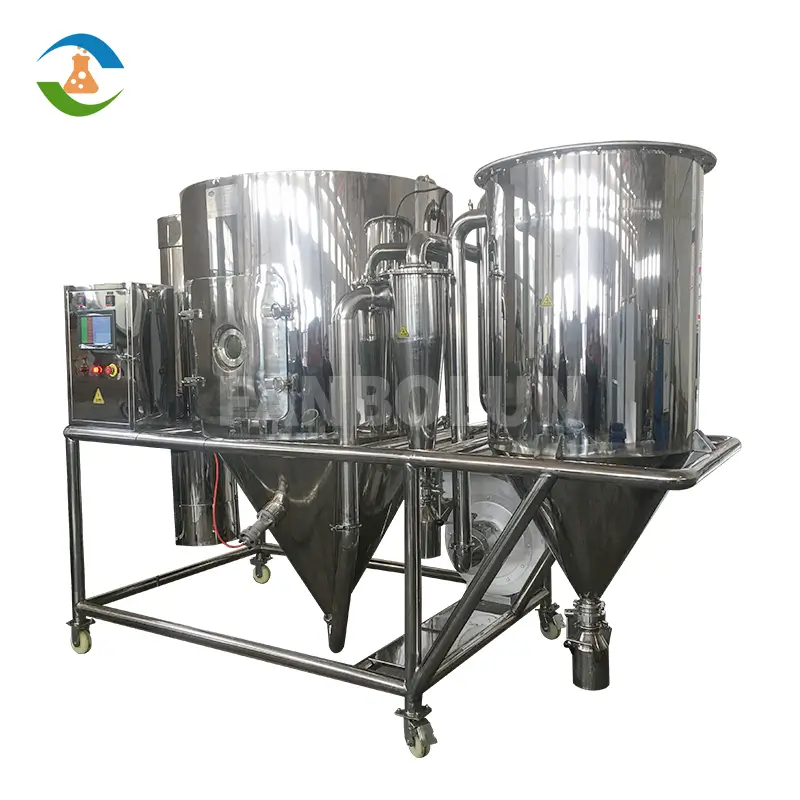
Differences between SD-2L and LPG-5L/10L Centrifugal Spray Dryers:
Atomization Method: The SD-2L uses a pressure nozzle, suitable for laboratory or small-scale production; the LPG-5L/10L uses an electric high-speed centrifugal atomizer, suitable for large-scale production.
Processing Capacity: The LPG series, with its larger capacity, offers stronger processing capabilities and is suitable for industrial production; the SD-2L is more appropriate for small-scale or research applications.
Application Scenarios: Both are suitable for drying various materials, but the SD-2L may be better for high-viscosity or special materials, while the LPG series is more versatile.
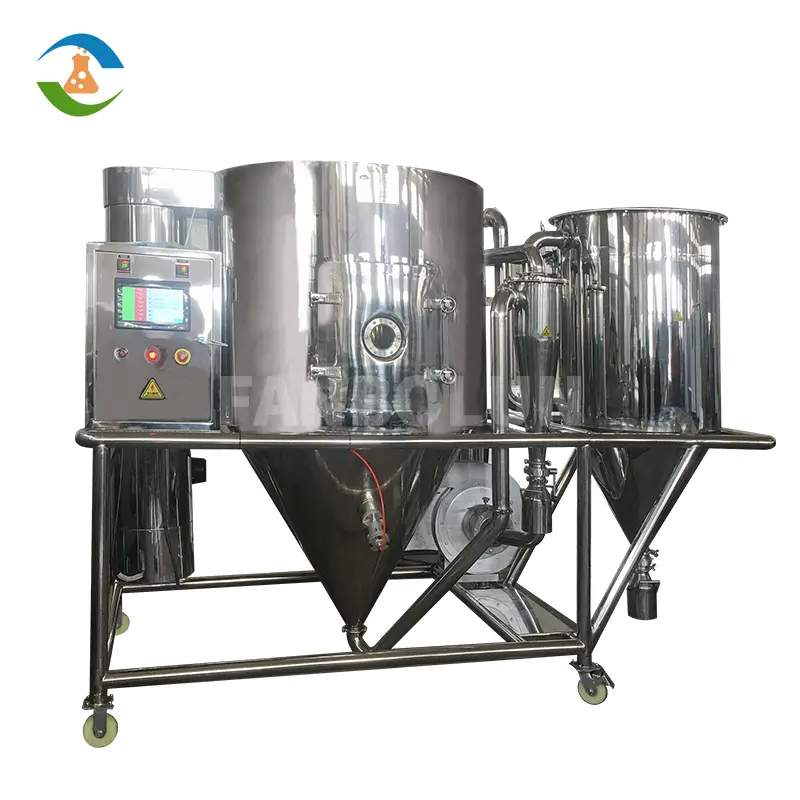
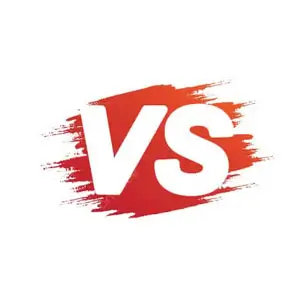
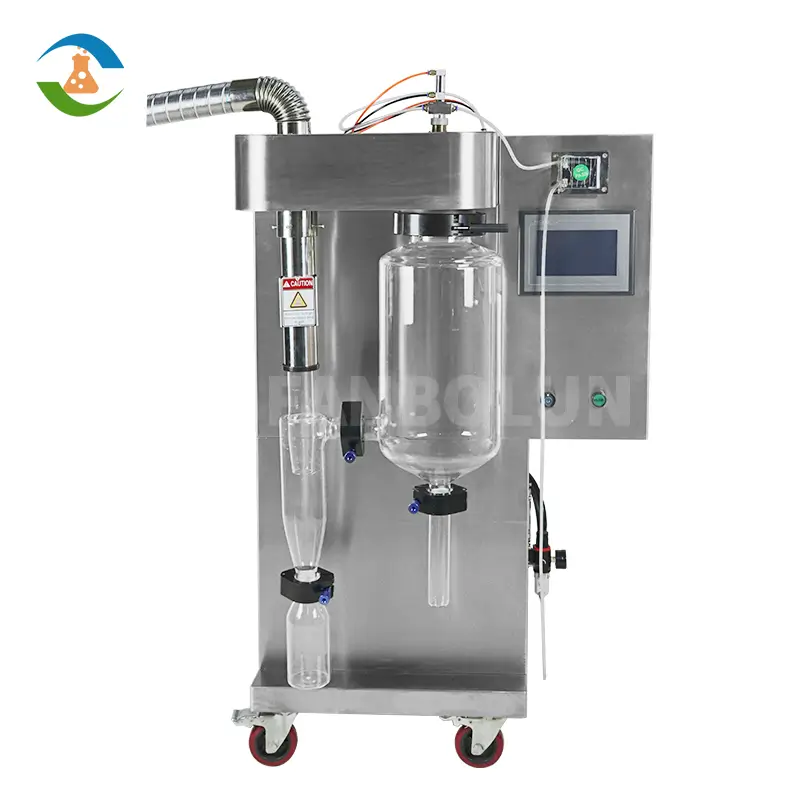
Regardless of whether it's pressure or centrifugal spray, the basic principle remains the same: atomizing the liquid material into fine droplets and rapidly drying them with hot air. The main difference lies in the atomization mechanism—pressure spray relies on pressure, whereas centrifugal spray depends on rotational force. This affects the droplet characteristics and the final product quality.
Features:
High-Precision Control System: The LPG-10L industrial spray dryer is equipped with an advanced PLC control system, combining real-time monitoring and automatic adjustment of temperature, humidity, and airflow speed to ensure stable product quality for each batch, meeting the most stringent production standards.
Efficient Thermal Energy Utilization: It adopts an optimized hot air circulation system, effectively reducing heat loss, improving energy utilization, and lowering operating costs. Precise control of the inlet air temperature and airflow speed accelerates the drying process, shortening the production cycle.
Flexible Spray Design: Equipped with various nozzle options, the spray angle and droplet size can be adjusted according to material characteristics to achieve the best atomization effect, ensuring uniform and fine particles that meet different product particle size requirements.
Precise Residual Moisture Control: The unique drying chamber design and efficient dehumidification system accurately control the residual moisture content in the finished product, preventing moisture absorption and deterioration, and ensuring the long-term stability of product storage.
Easy Cleaning and Maintenance: The equipment features a reasonable structure design, easy disassembly, and cleaning, complying with GMP and FDA international standards, ensuring production environment hygiene and safety, and reducing the risk of cross-contamination.
Intelligent Operation Interface: The user-friendly touch screen interface supports remote monitoring and fault diagnosis, reducing manual intervention and improving production efficiency and equipment utilization.
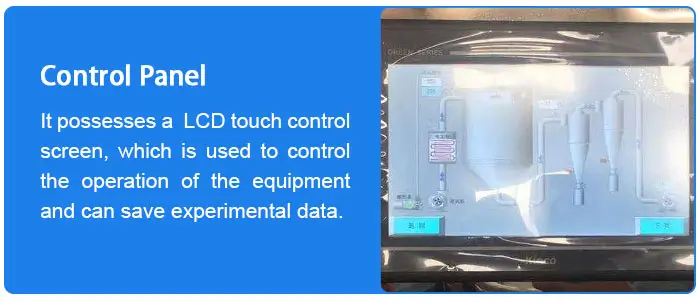
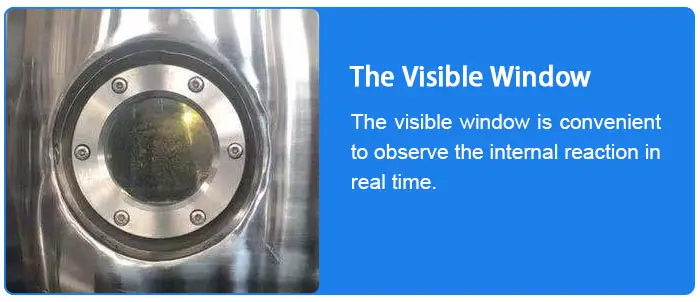
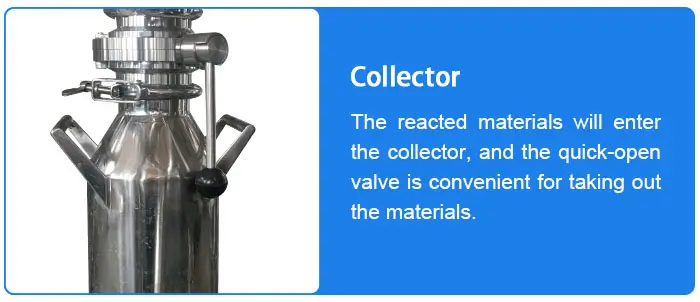
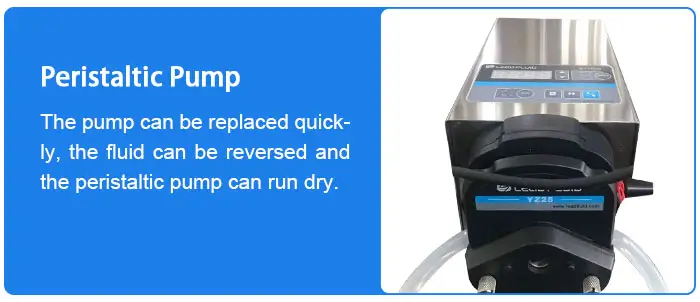
Applications:
Chemical Industry:
Polymers and resins: such as ABS emulsion, urea-formaldehyde resin, phenolic resin, etc.
Dyes and pigments: such as disperse dyes, reactive dyes, etc.
Inorganic chemicals: such as polyaluminum chloride, calcium carbonate, potassium sulfate, etc.
Catalysts and auxiliaries: including organic and inorganic catalysts.
Food Industry:
Dairy products: such as milk powder, whey powder, etc.
Proteins: such as egg powder, bone powder, soy protein, etc.
Seasonings: such as seasonings, flavors, vegetable juices, etc.
Sugars: such as glucose, maltose, etc.
Pharmaceutical Industry:
Suitable for drying various pharmaceutical raw materials, such as vitamins, amino acids, etc., particularly for heat-sensitive drugs, ensuring the active ingredients are not damaged.
Common Issues and Solutions:
1. Why has the evaporation rate decreased?
Causes:
Insufficient intake air speed.
Low inlet air temperature.
Leakage in the air supply system.
Solutions:
Increase air intake flow: Check and clean the air intake channel, adjust or repair the blower to ensure unobstructed airflow.
Check heating elements: Ensure they are functioning correctly and adjust to the appropriate temperature. Enhance insulation measures to reduce heat loss.
Ensure good system sealing: Inspect and tighten all joints and connections, replace damaged seals to prevent leaks.
2. Why does powder stick to the drying chamber walls?
Causes:
Drying speed is not fast enough.
Insufficient preheating temperature.
Improper control of feed speed.
Uneven evaporation of slurry.
Solutions:
Increase drying speed: Reduce the slurry feed speed or increase the inlet air temperature.
Proper preheating: Adjust the preheating temperature to the appropriate range to ensure it meets the required preheating temperature.
Control feed speed: Gradually increase the feed speed from slow to fast.
Regular inspection and cleaning: Regularly check and clean the slurry feed pipe and disc to ensure there are no blockages.
3. What to do if the industrial spray dryer discharge is unstable?
Causes:
Improper adjustment of feed speed, causing flow fluctuations.
Poor nozzle working condition, possibly worn or clogged.
Solutions:
Adjust the controller: Adjust the feed system controller to ensure a stable feed speed that meets process requirements.
Regular inspection: Regularly check the nozzle condition, clear any blockages, and replace worn nozzles if necessary.
4. Why is there significant noise during operation?
Causes:
Bearings of the fan or other rotating parts are damaged, causing unstable operation.
Loose fasteners inside the equipment, leading to mechanical vibrations.
Solutions:
Shutdown inspection: Shut down and inspect the bearings of the fan and other rotating parts; replace any damaged bearings promptly.
Tighten components: Conduct a thorough inspection of the equipment, tighten all loose components, and reduce vibration sources.
Product Parameters
Model | LPG-10 |
Inlet temperature(°C) | 140-350 |
Outlet temperature(°C) | 80-90 |
Moisture maximum evaporation (kg/h) | 10 |
Rotation form of centrifugal spray head | Mechanical transmission |
Rotating speed (r.p.m) | 25000 |
Diameter of spray disc (mm) | 50 |
Heat source | Electricity |
Electric heating power (kw) | 20 |
Length×width×height(m) | 3.2x1.5x2.4 |
Dry powder recovery rate(%) | ≥95 |
Model | LPG-10 |
Inlet temperature(°C) | 140-350 |
Outlet temperature(°C) | 80-90 |
Moisture maximum evaporation (kg/h) | 10 |
Rotation form of centrifugal spray head | Mechanical transmission |
Rotating speed (r.p.m) | 25000 |
Diameter of spray disc (mm) | 50 |
Heat source | Electricity |
Electric heating power (kw) | 20 |
Length×width×height(m) | 3.2x1.5x2.4 |
Dry powder recovery rate(%) | ≥95 |