Spary Drying Machine Pilot Plant
- Model: LPG-5L
- Moisture Evaporation : 5Kg/H
- Power(kW): 9kW
- Temp. Accuracy: 0.1℃
- Length×Width×Height (m): 1.8×0.93×2.2
- Dry Powder Recovery Rate(%): ≥95
Ideal for small labs and pharmaceutical production, the LPG-5L spray dryer converts liquids to powders with a 5L capacity. Perfect for chemical research and small-scale manufacturing. Efficient, reliable, and easy to operate.
Introduction
The LPG-5L spray drying machine, a remarkable representation of modern liquid shaping and drying technology, is designed for efficient and precise processing of solutions, emulsions, suspensions, and plastic paste materials. Its outstanding spray drying process can directly transform liquid raw materials into powdery, granular, or block solid products. Widely used in food, pharmaceutical, chemical, ceramics, and new material industries, this model, with its 5-liter capacity, meets the needs of both laboratory research and small-scale production, making it a highly esteemed precision device in the industry.
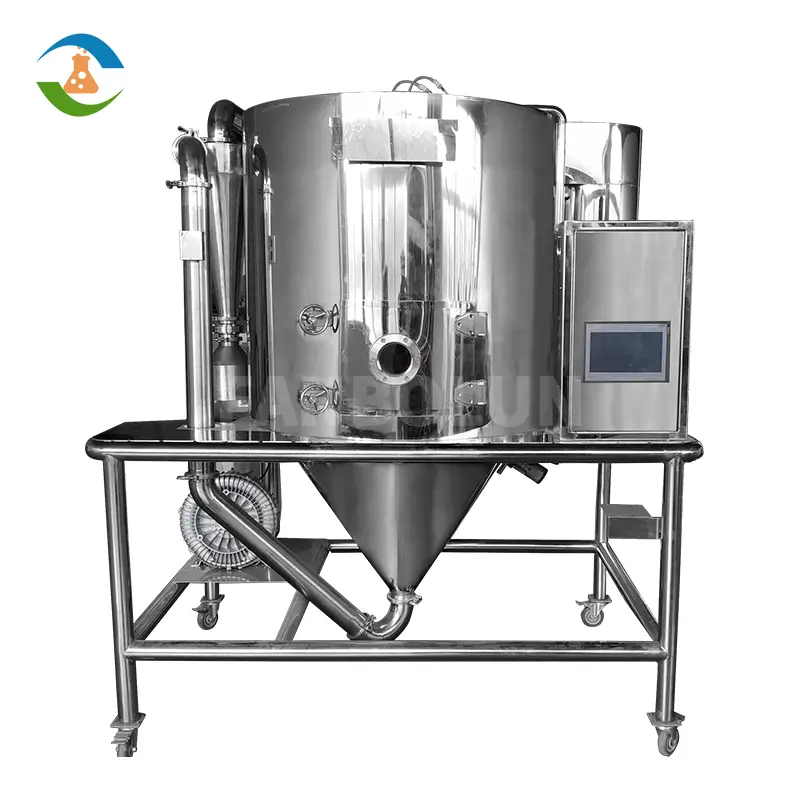
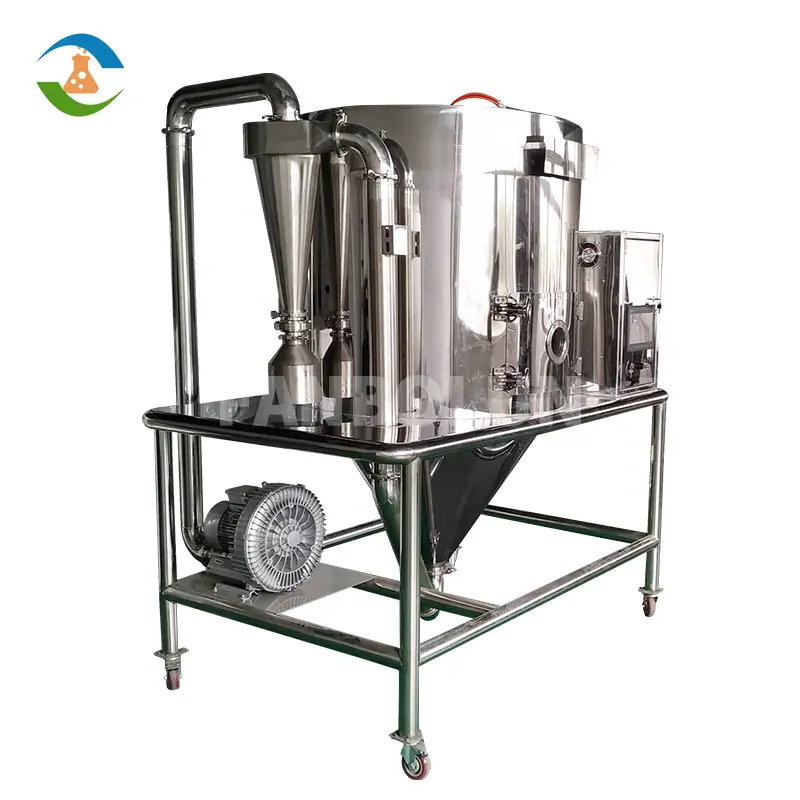
Features:
High-Efficiency Quick Drying: Instant atomization, increased surface area, evaporates 95%-98% of water in seconds, ideal for heat-sensitive materials.
Excellent Quality: Uniform products with good flowability, strong solubility, high purity, and superior quality.
Simplified Process: One-step drying into powder particles, eliminating subsequent processes, enhancing efficiency and purity.
Energy Saving and Eco-Friendly: Efficient heat recovery, low noise, low emissions, and green production.
Easy Maintenance: Reasonable design, easy to clean, stable long-term operation.
Versatility: Suitable for various materials, flexible adjustment of process parameters, meeting diverse needs.
Safe and Reliable: Multiple safety protections, ensuring safe operation and stable equipment reliability.
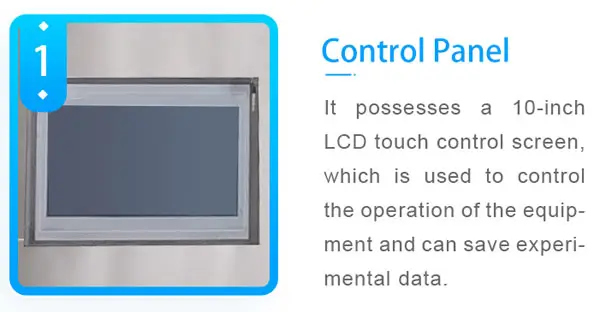
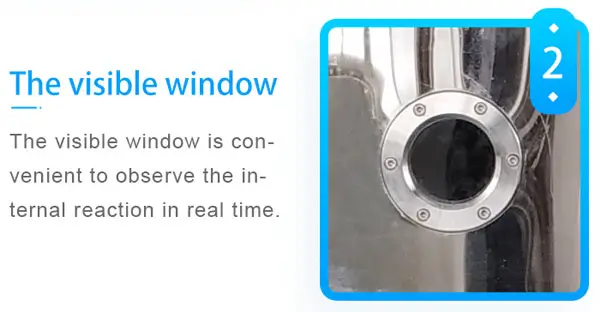
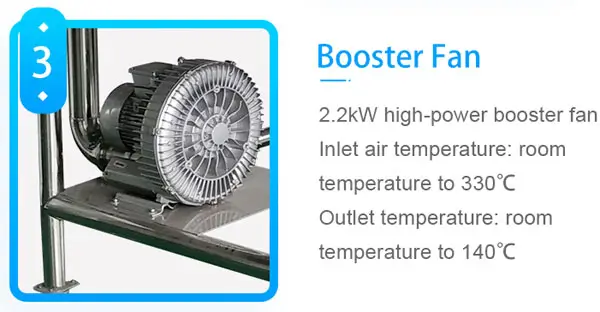
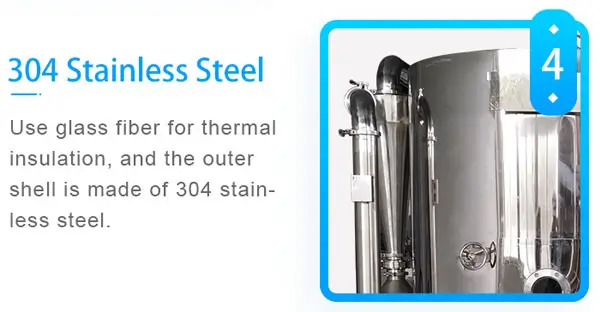
Applications:
Food Industry
Drying Food Raw Materials: In the food industry, laboratory spray drying machines are commonly used for producing milk powder, egg powder, coffee powder, juice powder, etc. Their unique drying method maximizes the retention of nutritional components and taste, ensuring product quality.
Preparation of Food Additives and Ingredients: The equipment can also be used for preparing various food additives such as flavors, colors, preservatives, and food ingredients like seasonings, nutritional enhancers, and vitamins. By spray drying the solution of additives or ingredients, high purity and stable powders or granules can be obtained, improving product quality and stability.
Pharmaceutical Industry
Production of Pharmaceutical Raw Materials and Herbal Extracts: In the pharmaceutical field, laboratory spray drying pilot plants are used for producing pharmaceutical raw materials and herbal extracts. The advantages of spray drying technology, such as fast drying speed and high product purity, make it ideal for drying pharmaceuticals.
Preparation of Nanomedicine: The equipment can also be used for preparing nanomedicines. By controlling the parameters during the spray drying process, nano-sized particles with specific sizes and shapes can be obtained, enhancing the bioavailability and efficacy of the medicine.
Chemical Industry
Production of Powdery and Granular Chemical Products: In the chemical field, laboratory spray drying pilot plants are widely used for producing various powdery and granular chemical products such as catalysts, pigments, and dyes. These products require high drying efficiency and purity, which spray drying technology can provide.
Synthesis and Preparation of New Materials: In the synthesis and preparation of new materials, laboratory spray drying pilot plants also play a crucial role. Spray drying technology allows for the rapid production of powdery or granular new material samples, shortening the research and development cycle.
Working Principle:
Clean air first passes through a precision filter to remove impurities, then enters the heater for preheating. It then spirally and uniformly enters the dryer. Simultaneously, the feed liquid is accurately delivered to the centrifugal atomizer at the top of the dryer by a specialized feed pump, where it is instantly dispersed into countless tiny droplets. These droplets fully contact with the concurrent hot air, undergoing efficient heat and mass exchange, rapidly evaporating moisture, and transforming into dried solid particles in a short time. The finished particles are finely collected in the bottom collection barrel via the cyclone separator, while the treated exhaust gas is discharged through the fan. The entire process is highly automated and easy to operate, improving production efficiency and ensuring high-quality product output.
Product Structure Diagram and Part Description:
Part No. | Part Name | Part No. | Part Name |
1 | Air Inlet | 2 | Electric Heating Tube |
3 | Observation Window | 4 | Control Cabinet |
5 | Temperature Control Seat | 6 | Atomizer |
7 | Cyclone | 8 | Pneumatic Hammer |
9 | Material Barrel | 10 | Stand |
Maintenance of LPG-5 Spray Drying Machine:
How to Regularly Clean the Main Unit of the LPG-5L Spray Drying Pilot Plant?
Regular cleaning of the main unit involves opening the door and carefully removing all connecting pipes to thoroughly clean the inner walls and pipes of the main unit. Ensure all parts are properly repositioned after cleaning to avoid affecting performance.
How to Clean the Spray Head After Each Experiment?
Before each experiment, flush the spray head with water (or a specific solvent that can dissolve the material) to ensure the internal pipes are clean. Then, remove the pump head and meticulously clean the nozzle and casing to prevent residue from affecting the next experiment.
How Often Should the Filter Screen of the Fan Inlet Be Cleaned?
It is generally recommended to clean the filter screen every 24 hours, but the frequency can be adjusted based on the type of material used. Regularly checking and cleaning the filter screen can prevent residue buildup, ensuring smooth fan operation and air quality.
How to Adjust Before Starting the Equipment to Ensure Complete Moisture Evaporation?
After connecting the power and starting the equipment, wait for the inlet and outlet temperatures to stabilize (preferably above 90 degrees Celsius at the outlet). First, pass water through the system and adjust the feed speed until no water droplets are observed on the tower walls, ensuring complete spray drying of the moisture. Then start the formal feeding process for the experiment.
How to Avoid Clogging When Stopping Feeding?
When stopping feeding, immediately flush the pump with water to prevent residual material from solidifying into powder at high temperatures and clogging the feed tube. After flushing, stop the heating and water supply, and wait for the equipment temperature to drop below 50 degrees Celsius before turning off the power.
How to Handle Sudden Situations During the Experiment?
If the feed suddenly stops during the experiment, immediately check the material in the pump to prevent solidification and clogging. If the power supply is suddenly cut off, quickly shut down the heating system to prevent overheating damage. Also, closely monitor the outlet temperature and fan air flow changes. If the outlet temperature suddenly drops significantly or continues to drop, or the fan air flow decreases, it may indicate internal clogging or failure. Stop the machine and check and clean immediately.
Common Problems and Solutions:
Here are detailed solutions to common issues encountered during the use of the spray drying machine:
1. Why is there excessive moisture in the product?
Cause:
Insufficient drying speed of the slurry: The heat exchange efficiency during the drying process is not high enough, causing the moisture in the slurry to not fully evaporate.
Solutions:
Reduce slurry feed speed: By slowing down the feed speed, each batch of slurry can stay in the drying chamber longer, allowing more time for thorough drying, ensuring complete moisture evaporation.
Increase input air temperature: Raising the temperature of the hot air entering the dryer can improve the heat exchange efficiency with the slurry, causing moisture to evaporate faster and speeding up the drying process.
2. Why is there an excessive amount of impurities in the dried material?
Cause:
Air filter malfunction.
High impurity content in the slurry itself.
Inadequate machine cleaning.
Solutions:
Check and maintain the air filter: Regularly inspect whether the air filter is clogged or incorrectly installed, ensuring it effectively filters out dust from the air. Replace or repair the air filter as needed.
Pre-treat the slurry: Pre-treat the slurry before drying, such as sieving, sedimentation, or filtration, to remove impurities and reduce the impurity content in the dried material.
Enhance machine cleaning: After each use of the drying machine, perform thorough cleaning and maintenance to ensure no residual impurities are left. Establish a standard operating procedure for cleaning to ensure every cleaning meets the required standards.
3. Why does the centrifugal atomizer disc vibrate during high-speed rotation?
Cause:
Residues on the atomizer disc.
Shaft deformation.
Solutions:
Clean the atomizer disc: After shutting down, thoroughly clean the atomizer disc to remove residues.
Replace the shaft: If the shaft is deformed, replace it promptly and ensure proper installation.
4. Why is the dried powder too fine?
Cause:
The concentration of solid components in the slurry is too low.
The feed speed of the centrifugal atomizer is set too high.
Solutions:
Adjust slurry concentration: Pre-treat the slurry before drying to reduce its moisture content or increase the proportion of solid components.
Optimize centrifugal atomizer parameters: Reduce the rotational speed of the centrifugal atomizer, so the atomized droplets are larger, resulting in larger particles after drying.
Note:When making any parameter adjustments, be sure to fine-tune according to the specific performance of the equipment and production requirements to avoid causing new problems due to excessive adjustments. After making adjustments, it is recommended to conduct multiple tests to verify the effect of the adjustments, ensuring the particle size of the powder meets the desired standards and production requirements.
Product Parameters
Model | LPG-5 |
Inlet temperature (°C) | 140-350 |
Outlet temperature (°C) | 80-90 |
Moisture maximum evaporation (kg/h) | 5 |
Rotation form of centrifugal spray head | Compressed air transmission |
Rotating speed (r.p.m) | 25000 |
Diameter of spray disc (mm) | 50 |
Heat source | Electricity |
Electric heating power (kw) | 9 |
Length×width×height (m) | 1.8×0.93×2.2 |
Dry powder recovery rate(%) | ≥95 |
Model | LPG-5 |
Inlet temperature (°C) | 140-350 |
Outlet temperature (°C) | 80-90 |
Moisture maximum evaporation (kg/h) | 5 |
Rotation form of centrifugal spray head | Compressed air transmission |
Rotating speed (r.p.m) | 25000 |
Diameter of spray disc (mm) | 50 |
Heat source | Electricity |
Electric heating power (kw) | 9 |
Length×width×height (m) | 1.8×0.93×2.2 |
Dry powder recovery rate(%) | ≥95 |