Laboratory Mini Small Spray Dryer
- Model: SD-2L
- Moisture Evaporation : 0-2Kg/H
- Power(kW): 4.4kW
- Temp. Accuracy: 0.1℃
- Length×Width×Height (m): 0.65×0.5×1.5
- Dry Powder Recovery Rate(%): ≥95
Ideal for small labs and product development, the SD-2L spray dryer efficiently converts various liquid materials into fine powders, featuring a 2L capacity, oil-free air compressor, and real-time PID temperature control.
Introduction
The SD-2L laboratory spray dryer is a valuable assistant in laboratory research and product development, designed for efficiently and precisely converting various liquid materials directly into fine, uniform micro-powders. Its outstanding feature is the ability to handle a wide range of solutions, including emulsions and suspensions, without the need for cumbersome pre-treatment steps such as filtering, concentrating, and pre-grinding. This greatly simplifies the operational process, enhancing experimental efficiency and flexibility.
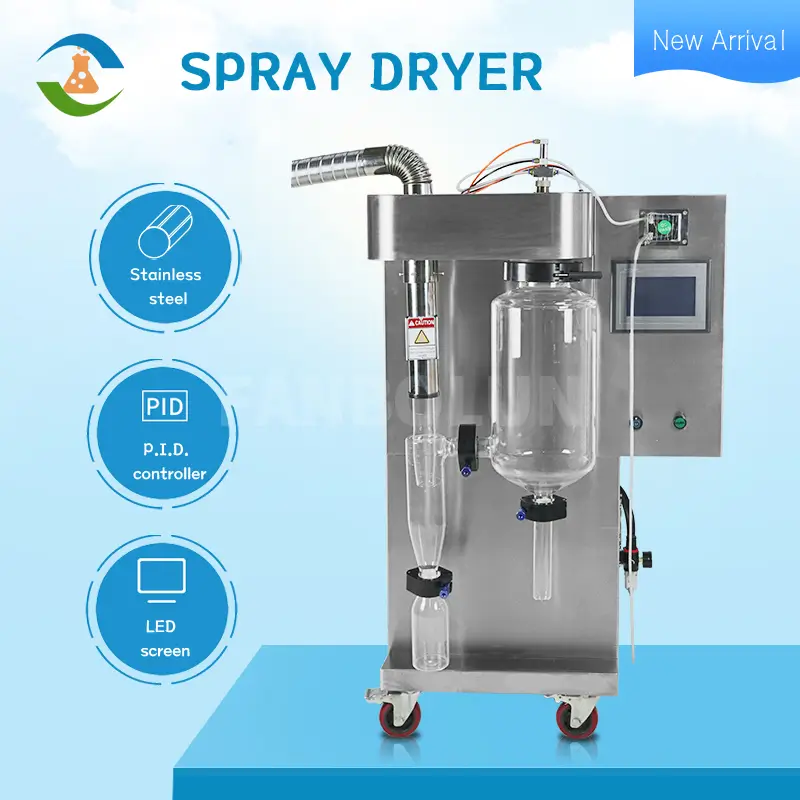
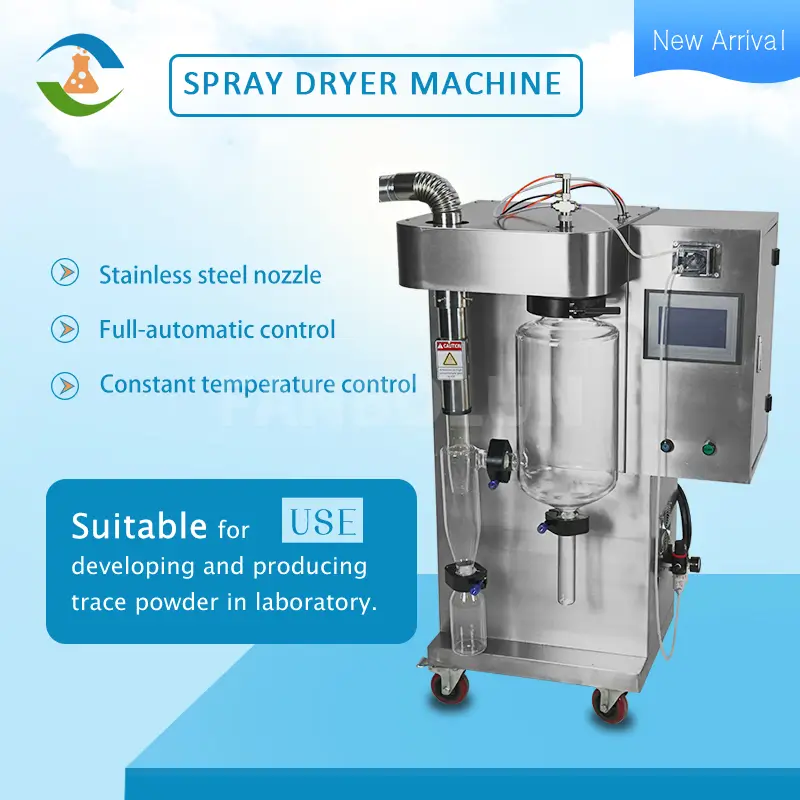
Features
The SD-2L small spray dryer boasts a range of remarkable characteristics and advantages, making it ideal for scientific research, teaching, and small-scale production applications. Below is a detailed analysis of its features:
High-Quality Transparent Material: The drying chamber and collection device are made from high-quality high-temperature borosilicate glass, which is not only heat-resistant but also offers excellent transparency. This allows the entire spray drying process to be fully visualized. This design ensures a contaminant-free and stable experimental environment, enabling researchers to observe and control the experiment intuitively, promptly identify and adjust issues, and improve the accuracy and efficiency of the experiments. All glass components are easy to disassemble and clean, facilitating maintenance and ensuring the long-term stable operation of the equipment and the reliability of experimental results.
Built-In Oil-Free Air Compressor: The equipment includes a built-in oil-free air compressor, ensuring that the powder remains free from oil contamination during the drying process, thereby guaranteeing product purity and quality. Additionally, the oil-free compressor features low noise levels (less than 60dB), meeting national laboratory noise standards and providing researchers with a quieter and more comfortable working environment. The powder has a uniform particle size distribution and good flowability, thanks to the compressor's stable performance and the optimized design of the mini spray dryer.
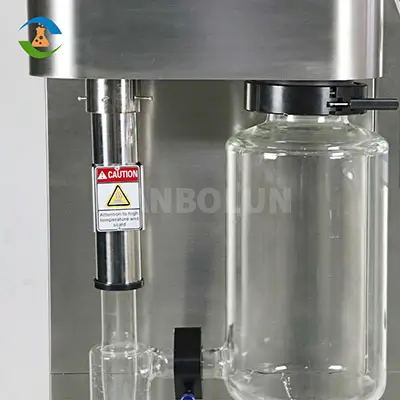
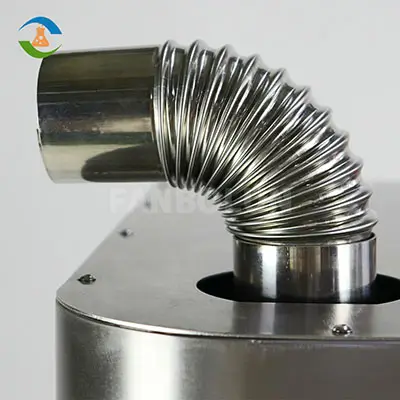
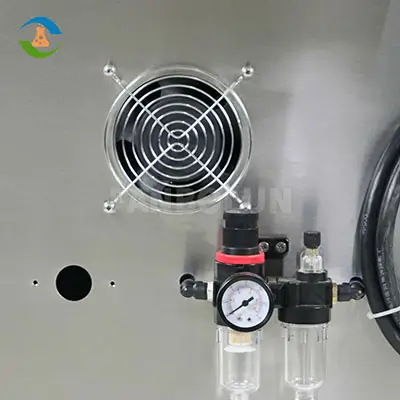
Dual-Fluid Spray Atomization Structure: The device employs a dual-fluid spray atomization structure made from high-quality 304 stainless steel. This structure ensures that the material is evenly atomized during the spray process. The stainless steel material is corrosion-resistant and heat-resistant, ensuring the long-term stable operation of the equipment.
Real-Time Adjustable PID Temperature Control Technology: The temperature control utilizes real-time adjustable PID temperature control technology, enabling precise control of the drying chamber temperature. PID control technology features fast response and high control accuracy, ensuring temperature stability and repeatability during experiments, thereby enhancing the reliability of experimental results.
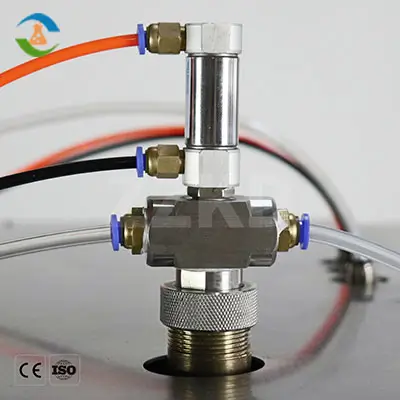
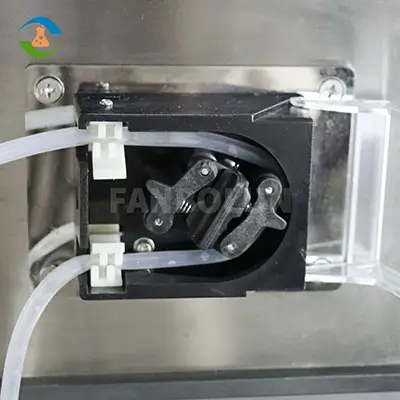
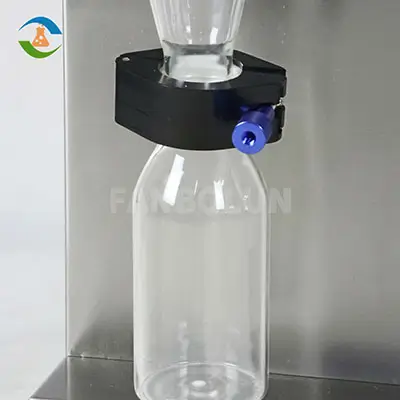
Fully Automatic and Manual Dual-Mode PLC Control: The equipment supports both fully automatic and manual operation modes, achieved through a PLC control system. The color touch screen display with both English and Chinese interfaces makes the device operation simpler and more intuitive. All parameters are displayed on an LCD screen, allowing researchers to monitor and adjust equipment parameters in real time easily.
Safety Protection Features: The device is equipped with comprehensive safety protection features, such as preventing the heater from starting if the fan does not start, effectively preventing safety accidents caused by equipment failure, ensuring the safety of the experimental process.
Applications
As a highly efficient, fast, and versatile experimental equipment, the laboratory laboratory spray dryer has applications across multiple industry fields. Here are specific scenarios where the small spray dryer is used:
Pharmaceutical Industry:
Used for drying raw materials such as traditional Chinese medicine, antibiotics, and pharmaceutical granules, ensuring that the active ingredients and efficacy of the drugs remain unaffected.
Due to its rapid drying speed, it is especially suitable for drying heat-sensitive drugs, effectively protecting the drug components.
Food Industry:
Applied in the drying of food ingredients such as seasonings, proteins, starch, dairy products, and coffee extracts, enhancing the shelf life and quality of the products.
Capable of preserving the original flavor and nutritional content of food, meeting the stringent requirements of the food industry.
Chemical Industry:
Suitable for drying chemical raw materials such as polymers, resins, dyes, and fragrances, improving product purity and quality.
Spray drying technology helps remove moisture and impurities from chemical raw materials, meeting the production demands of fine chemicals.
Working Principle
The SD-2L mini spray dryer uses a peristaltic pump to transport liquid containing solids to the dual-fluid spray nozzle. This nozzle integrates a cleaning needle to prevent clogging and maintains smooth operation by adjusting the needle frequency. Compressed air sprays the liquid into fine mist droplets, which enter the hot air drying chamber. The fine droplets, due to their high specific surface area, quickly exchange heat, with water vapor sublimating into dry particles. These particles are collected and separated from the exhaust gas by a cyclone separator, then enter the collection bottle. The exhaust gas is treated before being discharged. The droplet size is controlled by the flow rate of the compressed air, achieving efficient drying.
Product Structure and Component Description
Part No. | Part Name | Part No. | Part Name |
1 | Powder Collection Bottle | 2 | Cyclone Separation Bottle |
3 | Drying Chamber | 4 | Exhaust Pipe |
5 | Gas Interface | 6 | Atomizing Nozzle |
7 | Material Inlet | 8 | Control Box |
9 | Peristaltic Pump | 10 | Controller |
11 | Power Switch | 12 | Power Indicator Light |
13 | Material Receiving Tube |
Laboratory Spray Dryer User Instructions
I. Experimental Preparation
Installation Check: Please follow the installation instructions carefully to install each component, ensuring all connections are tight and secure with no omissions or looseness.
Start the Equipment:
Press the blue start button on the equipment to start the fan first, ensuring proper air circulation inside the device.
Then start the heater to provide the necessary heat for the drying process.
Set Parameters:
Use the control panel to set the desired inlet air temperature, a critical factor influencing the drying effect.
Wait for the equipment to preheat until the outlet air temperature reaches the set inlet air temperature.
Commissioning and Observation:
Before officially feeding the material, start the peristaltic pump in automatic mode and let the device run a test with water.
Observe the atomization effect of the material and the temperature changes. Adjust the fan speed and inlet air temperature settings based on actual conditions to achieve the best drying effect. Start feeding only after the system is running stably.
II. Operation Process
Once the system is stable and all parameters are set correctly, slowly feed the material to be dried into the spray gun through the peristaltic pump for spray drying.
Pay close attention to the material status inside the drying chamber and the exhaust gas at the outlet to ensure a smooth drying process.
III. Shutdown Steps
Clear the Pipeline:
When the material is used up or needs to be replaced, first use water to flush out any remaining material in the tubing (about 5 minutes) to avoid residue causing clogs or affecting future use.
Turn Off the Equipment:
Turn off the peristaltic pump to stop material feeding.
Turn off the air compressor to cut off the compressed air supply.
Turn off the heater to stop the heating process.
Cooling and Cleaning:
Wait for the inlet air temperature to drop below 40°C, then turn off the fan to let the equipment cool naturally.
Remove the collection bottle and transfer the dried material to another container for proper storage.
Clean the surface and internal residues of the equipment to keep it clean and dry, preparing it for the next use.
IV. Precautions
Continuously monitor the equipment's operating status and parameter changes to ensure safe and stable operation.
Regularly maintain and service the equipment, checking for worn or loose parts, and replace damaged components promptly.
Follow laboratory safety protocols to operate the equipment and prevent accidents.
Common Problems and Solutions
1. How to resolve severe wall-sticking issues?
Causes:
Excessive feed rate, leading to insufficient evaporation of the material.
Inadequate preheating of the drying chamber before spraying.
Excessive flow rate adjustment when starting the spray.
Unstable material liquid with poor flowability.
Solutions:
Reduce the feed rate to ensure the material fully evaporates.
Increase the inlet and outlet temperatures of the hot air to enhance drying effects.
Start with a small flow rate and gradually increase until the appropriate flow rate is reached.
Check and clean the pipeline, adjust the solid content of the material, and ensure good flowability of the liquid.
2. How to improve low product purity and high impurity levels?
Causes:
Poor air filtration, allowing impurities into the system.
Powder buildup mixing into the final product.
Low purity of raw materials.
Incomplete equipment cleaning, leaving residues that affect product purity.
Solutions:
Check and replace the filter material in the air filter, ensuring it is evenly laid and not used for too long.
Check and clean the scorched powder at the hot air inlet to avoid turbulence carrying in impurities; filter the liquid before spraying.
Use higher purity raw materials.
Thoroughly clean the equipment to ensure no residues affect product purity.
3. How to adjust when product powder is too fine?
Causes:
Low solid content in the material.
Insufficient feed rate.
Inadequate inlet air temperature, leading to fine particles.
Solutions:
Increase the solid content of the material to make particle formation easier and prevent fine particles.
Increase the feed rate to improve production efficiency.
Increase the inlet air temperature to promote particle drying and solidification, reducing fine powder production.
4. How to increase the yield of product powder?
Causes:
Poor separation effect of the cyclone separator.
Deformation of the separator due to impact or collision.
Poor airtightness at the separator's inlet and outlet, leading to powder escape.
Blockage in the inner wall and discharge port of the separator.
Solutions:
Check and repair the deformed cyclone separator to ensure its structural integrity.
Improve the airtightness of the separator's inlet and outlet to reduce powder escape.
Clean the inner wall and discharge port of the separator to keep them clear.
Consider adding a secondary dust removal device according to the powder characteristics and requirements to improve separation efficiency.
Product Parameters
Inlet air temperature: | Room temperature to 300°C |
Outlet temperature: | Room temperature to 140℃ |
Water evaporation capacity : | 0-2000ml/h |
Stainless steel nozzle: | Nozzle diameter Φ0.75mm |
Display: | 7-inch LCD touch operation display |
Real-time temperature control: | Error ±1℃ |
Real-time display temp. accuracy: | 0.1℃ |
Fan: | 0.75kW (aluminum alloy supercharged) |
Maximum drying air volume: | 105m³/h |
Inverter power: | 0.75kW |
Air compressor: | 0.55kW (oil-free) |
Whole machine power: | 2.2kW/4.4kW/8.8kW 220V |
Dimensions: | 650×500×1500mm |
Inlet air temperature: | Room temperature to 300°C |
Outlet temperature: | Room temperature to 140℃ |
Water evaporation capacity : | 0-2000ml/h |
Stainless steel nozzle: | Nozzle diameter Φ0.75mm |
Display: | 7-inch LCD touch operation display |
Real-time temperature control: | Error ±1℃ |
Real-time display temp. accuracy: | 0.1℃ |
Fan: | 0.75kW (aluminum alloy supercharged) |
Maximum drying air volume: | 105m³/h |
Inverter power: | 0.75kW |
Air compressor: | 0.55kW (oil-free) |
Whole machine power: | 2.2kW/4.4kW/8.8kW 220V |
Dimensions: | 650×500×1500mm |